Been busy with school work and all, couldn't get much done until middle of last week. So anyway here are the process:
The chairs are giving me a very hard time to work with because of the clay, since my fingers sweat a lot while working with it, which makes it difficult to work with the clay because water makes the clay go soft. So far, only managed to finish 2 out of 8 chairs.
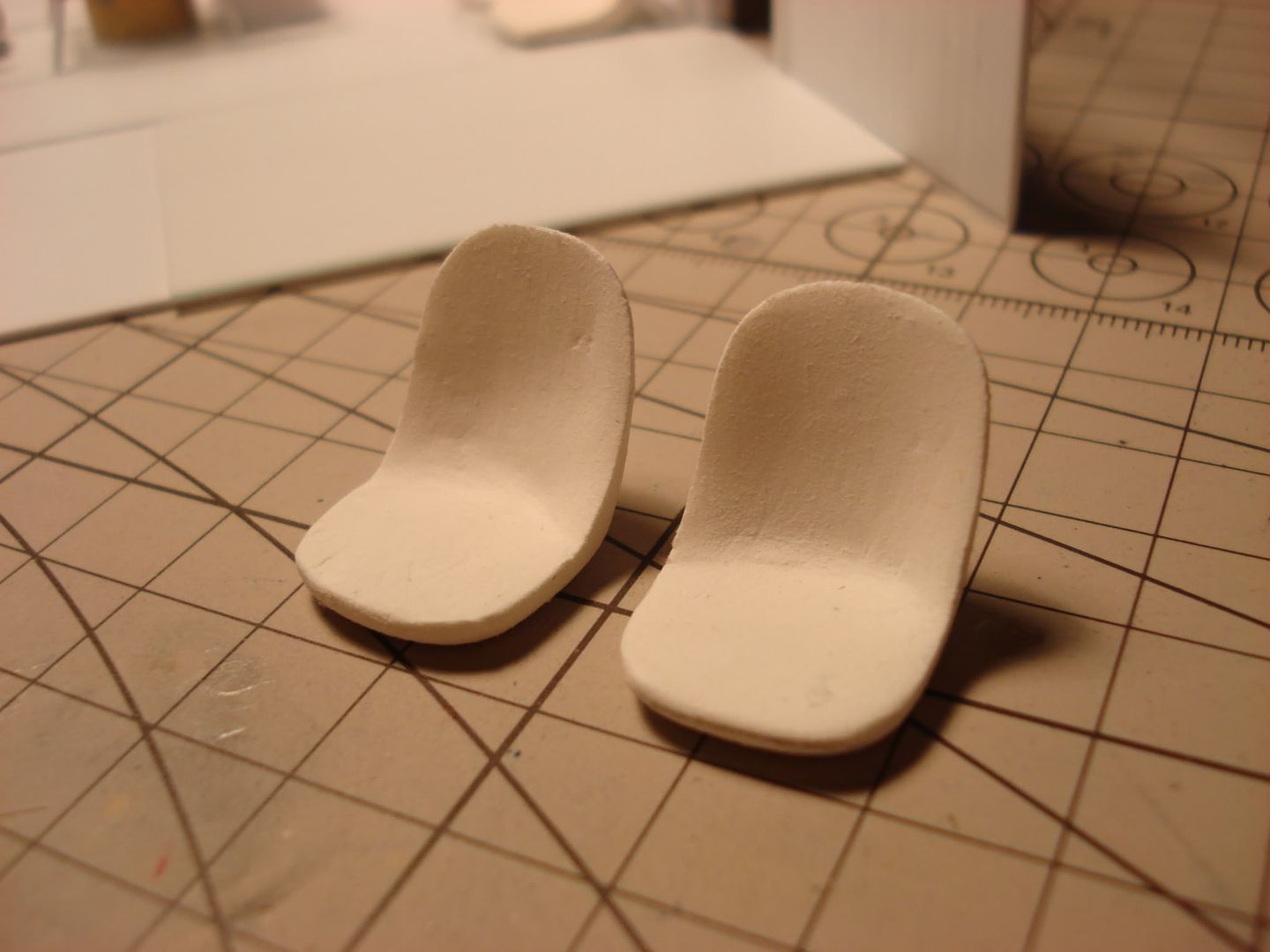
However, on the plus side, most of the major components of this project is done. Right now it requires a lot of details, such as bulletin board on the wall etc.
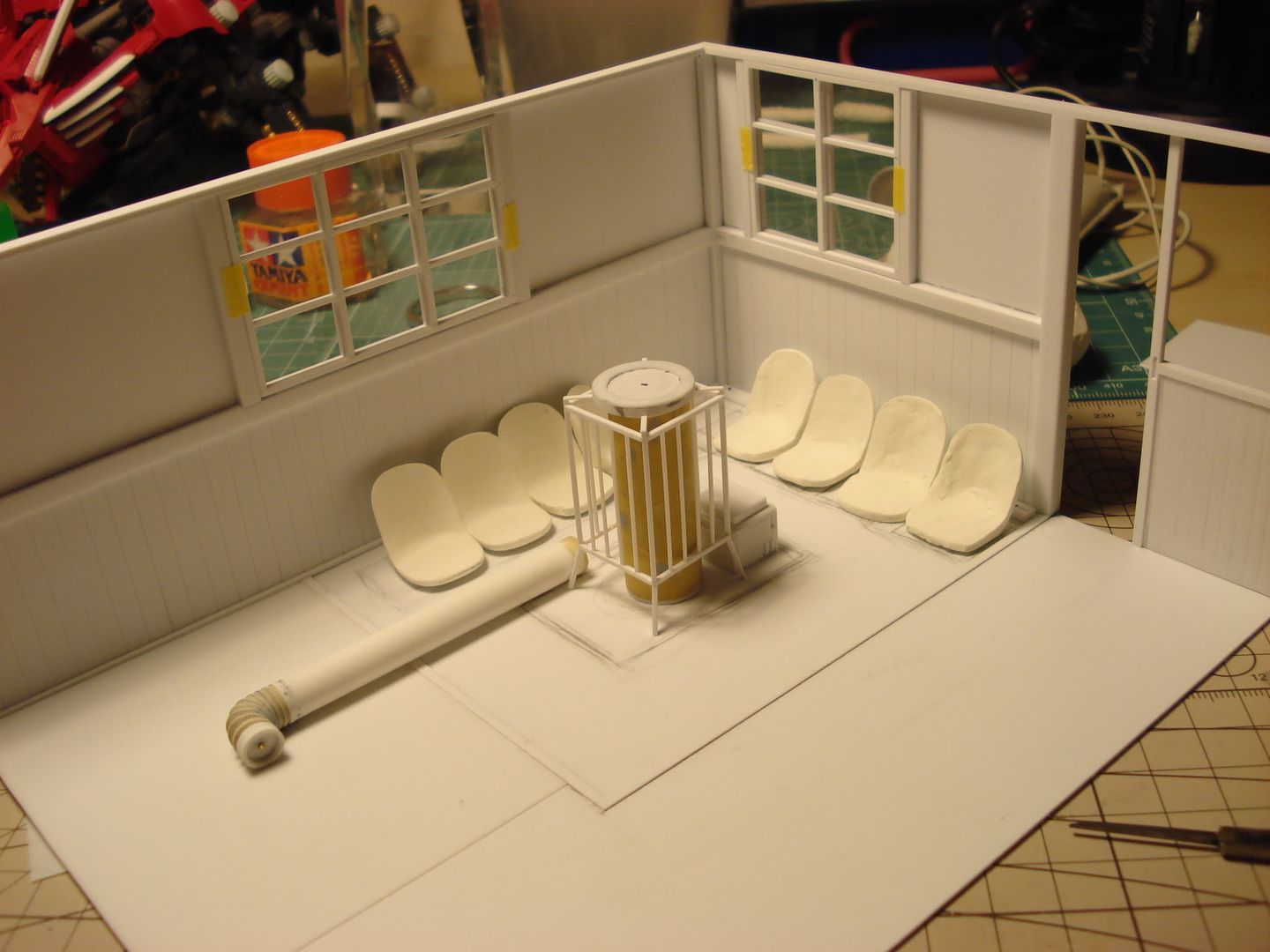
And here is the door:
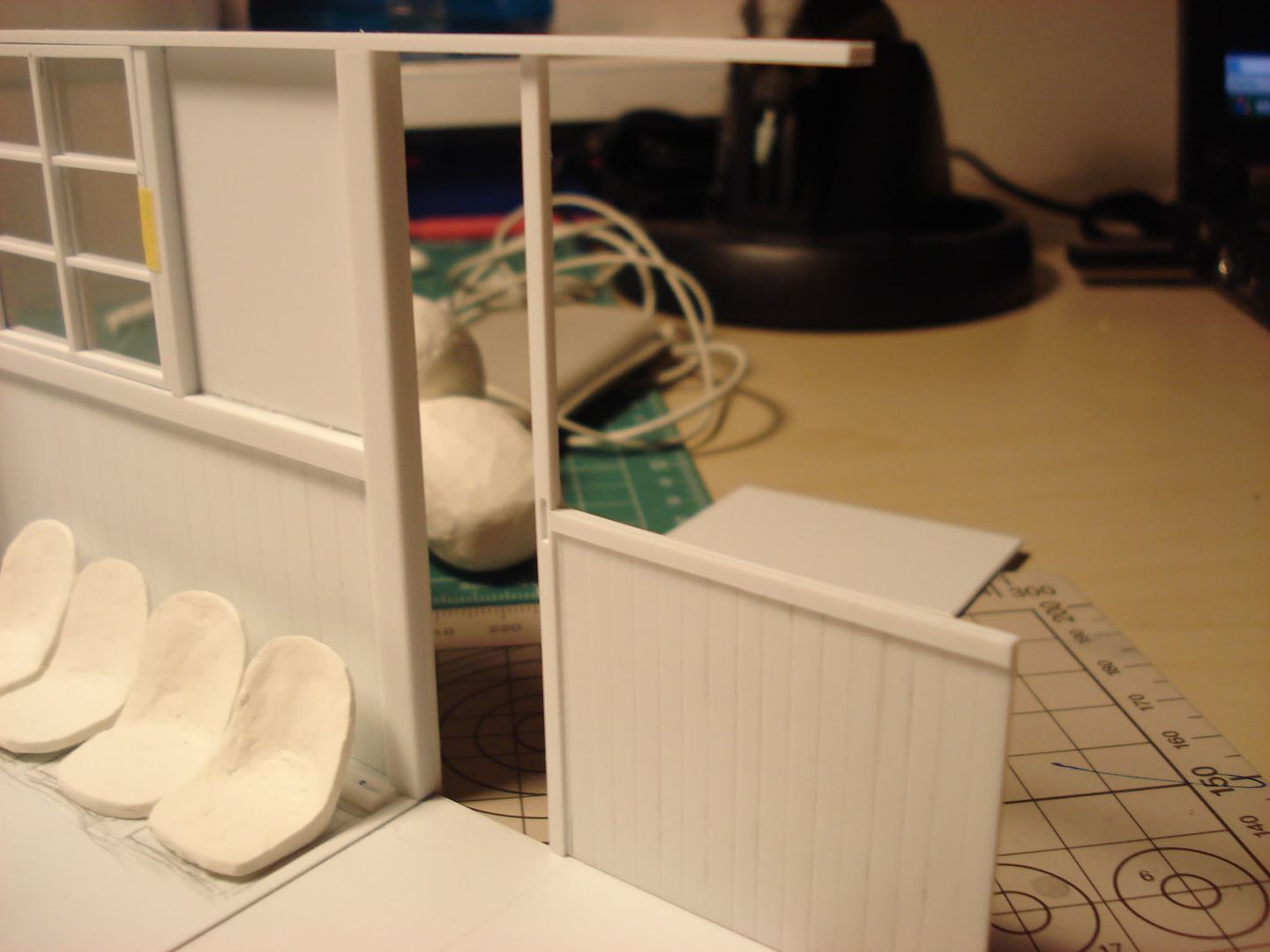
Here is the handle:
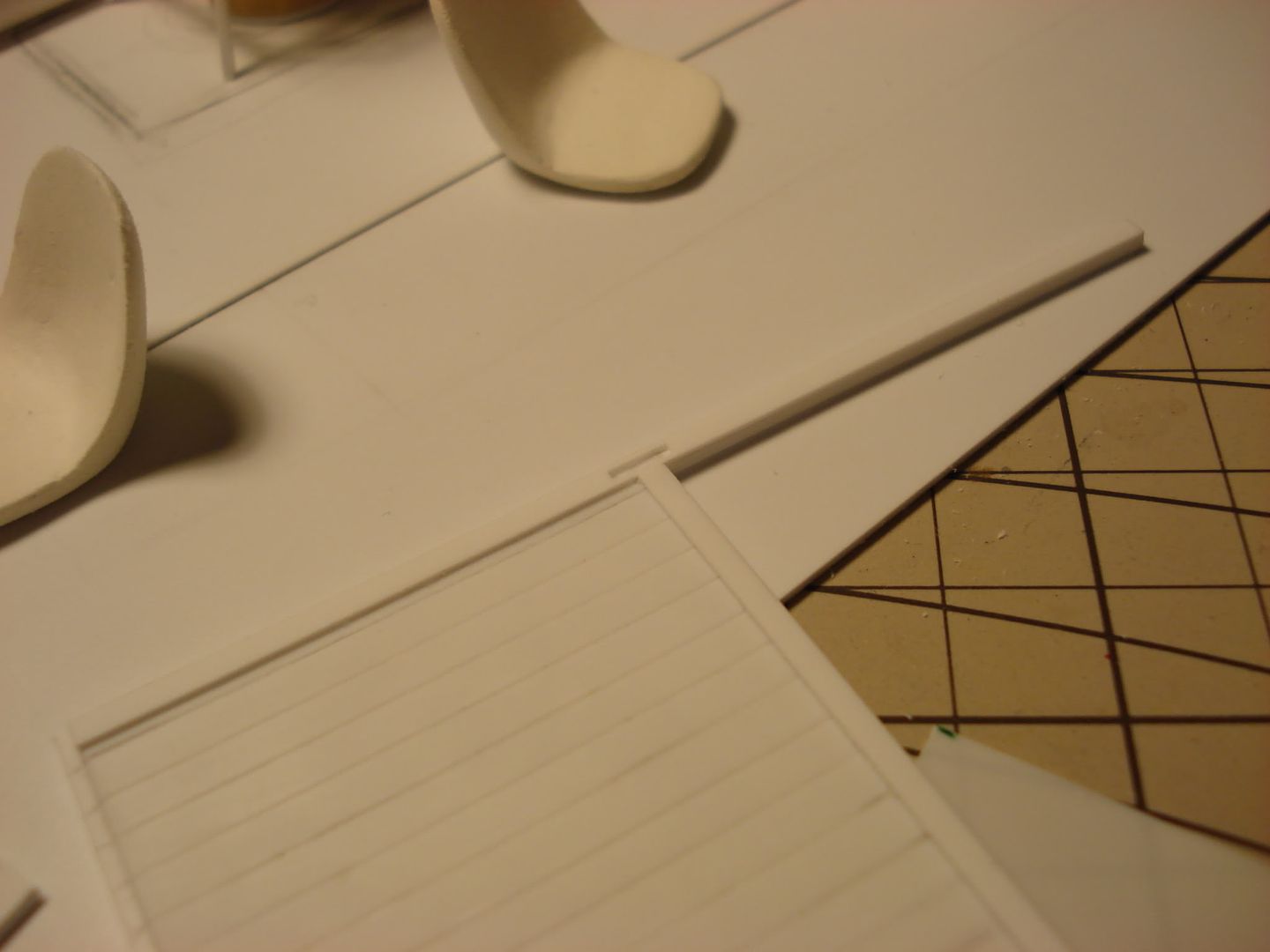
On the negative side, there won't be too much of an update until Jan because my camera will not be with me for a while. Hopefully I can find another one instead.
Oh, last but not least, Merry Christmas everyone!